PORTWELL PCI-AI12-16A

Description
Multifunction, high-speed, analog-to-digital converter board for use in PCI-Bus computers. It accepts up to 16 single-ended or eight differential inputs. Include foregoing plus includes a 2K Samples FIFO data buffer and a 2K words Point List FIFO buffer
Part Number
PCI-AI12-16A
Price
Request Quote
Manufacturer
PORTWELL
Lead Time
Request Quote
Category
I/O Products
Specifications
Categorization Information
IO Products
Features
- 16 Single-Ended / 8 Differential Analog Inputs
- 12-Bit Resolution, 100kHz A/D Converter
- Eight Programmable Voltage Ranges (Unipolar & Bipolar) and 4-20mA Current Range
- FIFO Data and Point List Buffers ('A' version). Both FIFOs 2K
- On-board Pacer Clock and Counter Timers
- Universal PCI, PCI-X, 3.3V and 5V compatible
- Number of Analog Inputs Can Be Expanded up to 256 by use of our External Signal Conditioners/Sub-Multiplexers
- Software Drivers Included for Windows 95/98/NT/2000/XP, and LabVIEW under Windows 95/98/NT
Datasheet
Extracted Text
MODEL PCI-AI12-16 USER MANUAL FILE: MPCI-AI12-16.Ff Notice The information in this document is provided for reference only. Portwell does not assume any liability arising out of the application or use of the information or products described herein. This document may contain or reference information and products protected by copyrights or patents and does not convey any license under the patent rights of Portwell, nor the rights of others. IBM PC, PC/XT, and PC/AT are registered trademarks of the International Business Machines Corporation. Printed in USA. Copyright 2001, 2005 by Portwell I/O Products Inc. All rights reserved. WARNING!! ALWAYS CONNECT AND DISCONNECT YOUR FIELD CABLING WITH THE COMPUTER POWER OFF. ALWAYS TURN COMPUTER POWER OFF BEFORE INSTALLING A CARD. CONNECTING AND DISCONNECTING CABLES, OR INSTALLING CARDS INTO A SYSTEM WITH THE COMPUTER OR FIELD POWER ON MAY CAUSE DAMAGE TO THE I/O CARD AND WILL VOID ALL WARRANTIES, IMPLIED OR EXPRESSED. Manual PCI-AI12-16/16A 2 Warranty Prior to shipment, Portwell equipment is thoroughly inspected and tested to applicable specifications. However, should equipment failure occur, Portwell assures its customers that prompt service and support will be available. All equipment originally manufactured by Portwell which is found to be defective will be repaired or replaced subject to the following considerations. Terms and Conditions If a unit is suspected of failure, contact Portwell' Customer Service department. Be prepared to give the unit model number, serial number, and a description of the failure symptom(s). We may suggest some simple tests to confirm the failure. We will assign a Return Material Authorization (RMA) number which must appear on the outer label of the return package. All units/components should be properly packed for handling and returned with freight prepaid to the Portwell designated Service Center, and will be returned to the customer's/user's site freight prepaid and invoiced. Coverage First Three Years: Returned unit/part will be repaired and/or replaced at Portwell option with no charge for labor or parts not excluded by warranty. Warranty commences with equipment shipment. Following Years: Throughout your equipment's lifetime, Portwell stands ready to provide on-site or in-plant service at reasonable rates similar to those of other manufacturers in the industry. Equipment Not Manufactured by Portwell Equipment provided but not manufactured by Portwell is warranted and will be repaired according to the terms and conditions of the respective equipment manufacturer's warranty. General Under this Warranty, liability of Portwell is limited to replacing, repairing or issuing credit (at Portwell discretion) for any products which are proved to be defective during the warranty period. In no case is Portwell liable for consequential or special damage arriving from use or misuse of our product. The customer is responsible for all charges caused by modifications or additions to Portwell equipment not approved in writing by Portwell or, if in Portwell opinion the equipment has been subjected to abnormal use. "Abnormal use" for purposes of this warranty is defined as any use to which the equipment is exposed other than that use specified or intended as evidenced by purchase or sales representation. Other than the above, no other warranty, expressed or implied, shall apply to any and all such equipment furnished or sold by Portwell. Manual PCI-AI12-16/16A 3 Table of Contents Chapter 1: Introduction...................................................................................................... 5 Specifications.................................................................................................................. 7 Figure 1-1: Block Diagram .........................................................................................................................9 Chapter 2: Installation...................................................................................................... 10 Chapter 3: Option Selection ............................................................................................ 12 Figure 3-1: Option Selection Map ............................................................................................................12 Chapter 4: Address Selection.......................................................................................... 13 Chapter 5: Programming.................................................................................................. 14 Programming regular card........................................................................................... 14 Table 5-1: Register addresses on normal card (hex)...............................................................................14 Programming the A card .............................................................................................. 18 Programming Guide...................................................................................................... 20 Interrupt Based or Background Data Acquisition...................................................... 21 FIFO Based Data Acquisition....................................................................................... 21 Interrupt-Based FIFO Mode.......................................................................................... 22 Chapter 6: Programmable Interval Timer ....................................................................... 23 Programming................................................................................................................. 24 Reading and Loading the Counters............................................................................. 25 Programming Examples............................................................................................... 27 Chapter 7: Calibration ...................................................................................................... 29 Chapter 8: Connector Pin Assignments......................................................................... 30 Table 7-1: Connector Pin Assignments....................................................................................................30 Manual PCI-AI12-16/16A 4 Chapter 1: Introduction These cards are multifunction high-speed analog-to-digital converter cards for use in 5-volt PCI bus computer slots. With these cards installed the computer can be used as a precision data acquisition and control system or as a signal analysis instrument. Description The card accepts up to eight differential or 16 single-ended analog input channels. Inputs are protected against over-voltage conditions up to +35 volts and typically survive static discharges beyond 4000 volts. The channel input configuration is software selectable. When using the card in differential mode the common mode rejection ratio is a minimum 80dB at 45KHz and the common mode voltage rejection capability is +11V. The input signals are amplified by an onboard instrumentation amplifier to provide voltage ranges of 10, 5, 1.25-6.25, and 1.25-3.75 volts unipolar and +10, +5, +2.5 and +1.25 volts bipolar. In addition, you can read 4- 20 mA current inputs by manually installing jumpers to utilize onboard resistors. In this case, the current input is converted to an analog voltage range of 1.25-6.25V with full 12-bit resolution and there can be up to eight inputs. Each channel must be dedicated to either voltage or current. These cards contain an industry standard 12-bit successive-approximation analog-to-digital converter (A/D) with a sample and hold amplifier input. Under ideal conditions throughput of over 100,000 conversions per second is possible. Model A has all of the foregoing plus a 2K samples FIFO data buffer and a 2K words point list buffer. These buffers give capability for full-speed counter-driven background data-acquisition with no computer interaction until the data FIFO needs draining. This allows 100,000Hz data to be taken with little processor overhead. A/D conversions may be initiated in any of three ways: (a) software command, (b) an on-board programmable timer, or (c) direct external trigger. In turn, data may be transferred to the computer by any of two software selectable methods: (a) polling for end-of-conversion (EOC), or (b) an EOC interrupt. In the A card a third method of data transfer is available, using the onboard storage FIFO. Input System Expansion These cards can be used with up to 16 external AIM-16P analog input expansion cards. Each AIM-16P card provides capability for 16 differential inputs and thus can be used to provide a maximum of 256 analog inputs per combination of analog input expansion cards and a single version of this card. The initial AIM-16Ps are connected to the card by a special cable adapter and ribbon cable. Additional AIM-16P units are connected by daisy-chaining with ribbon cables. In the normal system configuration each AIM-16P is connected to a single-ended input of the card. However, if interconnection cable noise becomes problematic or if long cables are required, then the AIM-16P cards can be connected to the differential inputs of the card. Using the differential connection allows better monitoring of remote locations because noise will be reduced by the common mode noise rejection capability of the card. Note: In this configuration, the maximum number of inputs that can be handled is 128. Note: If the VRef from the cards is to be used to power a bridge or other apparatus connected to the AIM-16, then pin 28 on J1 of the the card must be grounded. Consult the factory to obtain a specially modified card that implements this option. The control register at base address+3 provides channel and gain control bits for use with submultiplexers like the AIM-16. SEL3-SEL0 are typically used for channel, and G2-G0 are used for gain. If no submulitplexer Manual PCI-AI12-16/16A 5 is being used, it is a good idea to use SEL3-SEL0 as ID tags. These values will comprise the top four bits of the data returned from the a/d converter. Discrete Digital I/O Four bits of TTL/CMOS compatible digital I/O capability are provided. The four bits of digital output are available with LSTTL logic levels and have high current drive capability of 500mA per line. Counter/Timer The cards contain a type 8254 counter/timer that has three 16-bit programmable down counters. Counter/Timer 0 is enabled by a pin on the connector (CTR0) and uses an external clock of up to 10 MHz as selected by user software. Counter/Timers 1 and 2 are concatenated to form a 32-bit counter and receive 1 MHz clock inputs from an on-board crystal-controlled oscillator. The counter/timers can be set up for event counting, frequency or period measurements, and pulse or wave form generation. Also, Counter/Timers 1 and 2 can be programmed to initiate A/D conversions. A driver with source code is provided to facilitate use of the counter/timer chip in data acquisition applications. Interrupts These cards have interrupt capability within the PCI bus. The interrupt for the card can be software enabled and can be initiated by the completion of an A/D conversion, or in the A version, by various FIFO status conditions. Transferring Data into the Computer These cards have been designed to provide high data throughput using the PCI bus. Direct I/O transfers provide the easiest means of transferring the data to memory. This type of transfer allows data to be sent at rates of over 100,000 samples/second. Also, program transfers are subject to disruption by other interrupt processes in the computer. Use of real time triggering of the A/D assures synchronized sampling that is unaffected by other computer operations. That capability is essential in applications such as signal analysis, fast Fourier transform, and vibration and transient analysis where high data rates must be sustained for short intervals of time. The FIFO on the A version of the card allows the card to acquire data from a list of channels using a point-list FIFO and to store the data in the onboard data FIFO, eliminating most timing concerns. Reference Voltage and Power Required A +10V (+0.25) reference voltage is available from the A/D reference source for external use. This reference output can source up to 200 mA of current. The PCI-AI12-16(A) requires only +5VDC and +12VDC from the computer power supply. Manual PCI-AI12-16/16A 6 Specifications A/D Specification • Type: Successive approximation. • Resolution: 12 binary bits. • Conversion Time: 8 sec max., 5.7 sec typical. • Integral Linearity Error: +0.45 LSB maximum. • Differential Non-Linearity: No missing codes. • Monotonicity: Guaranteed over operating temperature range. • Linearity: +1 bit. • Zero Drift: +10 ppm/°C maximum. • Gain Drift: +45 ppm/°C maximum. • Trigger Source: Software selectable, external trigger, programmable timer, or program command. Sample and Hold Amplifier • Acquisition Time: 1 microsecond to 0.01% typical for full scale step function input. • Aperture Uncertainty: 0.3 nanosecond typical. Reference Voltage Output • Voltage: +10VDC +0.25VDC. • Temp. Coefficient: +30 ppm/°C. • Load Drive: +200mA maximum. Digital I/O Inputs • Logic high: 2.0 to 5.0 VDC at 20 uA maximum at 2.7V. • Logic low: -0.5 to +0.8 VDC at -0.4mA maximum. Output • Driver is ULN2003A, monolithic high-voltage, high-current Darlington transistor array. The collector-current rating of each Darlington pair is 500mA. Total of approximately 1.3A maximum for the four output lines at 25 °C .Applications include relay drivers, hammer drivers, lamp drivers, display drivers (LED and gas discharge), and line drivers. Manual PCI-AI12-16/16A 7 Programmable Timer • Type: 82C54-2 programmable interval timer. • Counters: Three 16-bit down counters, two permanently concatenated with 1MHz clock as programmable timer. • Output Drive: 2.2mA at 0.45V (5 LSTTL loads). • Input Gate: TTL/DTL/CMOS compatible. • Clock Frequency: DC to 10MHz. • Active Count Edge: Negative edge. • Min Clock Pulse Width: 30nS high/50nS low. • Timer Range: 2.5 MHz to <1 pulse/hr. Environmental • Operating Temp: 0 °C. to 50 °C. • Storage Temp: -20 °C. to +70 °C. • Humidity: 0 to 90% RH, non-condensing. • Power Required: +5VDC: 600 mA typical. +12VDC: 650 mA typical. -12VDC: 650 mA typical. Manual PCI-AI12-16/16A 8 UNI UNIPOLAR/ BIPOLAR VREF BIP SELECT 16 S.E./ 8 DIFF'L SWITCH SAMPLE/ CH0 HI HOLD 12 BIT A/D CONVERTER CH0 LO 1 A/D & MUX 16 S.E. 2 OR GAIN DATA REGISTER 4 MUX 8 DIFF'L SELECT 8 ANALOG INPUTS STATUS REGISTER CH15 MUX INCREMENT & CONTROL LOGIC GN0 I GN1 B 7 BIT GN2 DATA M OUTPUT INTERNAL DATA BUS SEL0 REGISTER (SUBMUX BUFFERS SEL1 P CONTROL) SEL2 C SEL3 I TRIGGER SELECT A/D TRIG B LOGIC ADDRESS U DECODE S & OP0 SELECT 4 BIT OP1 DIGITAL OP2 INPUT/OUTPUT OP3 CONTROL REGISTER INTERRUPT CONTROL Figure 1-1: Block Diagram Manual PCI-AI12-16/16A 9 Chapter 2: Installation A printed Quick-Start Guide (QSG) is packed with the card for your convenience. If you’ve already performed the steps from the QSG, you may find this chapter to be redundant and may skip forward to begin developing your application. The software provided with this card is on CD and must be installed onto your hard disk prior to use. To do this, perform the following steps as appropriate for your operating system. Configure Card Options via Jumper Selection Before installing the card into your computer, carefully read Chapter 3: Option Selection of this manual, then configure the card according to your requirements. Our Windows based setup program can be used in conjunction with Chapter 3 to assist in configuring jumpers on the card, as well as provide additional descriptions for usage of the various card options. CD Software Installation The following instructions assume the CD-ROM drive is drive “D”. Please substitute the appropriate drive letter for your system as necessary. DOS 1. Place the CD into your CD-ROM drive. 2. Type B- to change the active drive to the CD-ROM drive. 3. Type GLQR?JJ- to run the install program. 4. Follow the on-screen prompts to install the software for this board. WINDOWS 1. Place the CD into your CD-ROM drive. 2. The system should automatically run the install program. If the install program does not run promptly, click START | RUN and type BGLQR?JJ, click OK or press -. 3. Follow the on-screen prompts to install the software for this board. LINUX 1. Please refer to linux.htm on the CD-ROM for information on installing under linux. Caution! * ESD A single static discharge can damage your card and cause premature failure! Please follow all reasonable precautions to prevent a static discharge such as grounding yourself by touching any grounded surface prior to touching the card. Manual PCI-AI12-16/16A 10 Hardware Installation 1. Make sure to set switches and jumpers from either the Option Selection section of this manual or from the suggestions of SETUP.EXE. 2. Do not install card into the computer until the software has been fully installed. 3. Turn OFF computer power AND unplug AC power from the system. 4. Remove the computer cover. 5. Carefully install the card in an available 5V or 3.3V PCI expansion slot (you may need to remove a backplate first). 6. Inspect for proper fit of the card and tighten screws. Make sure that the card mounting bracket is properly screwed into place and that there is a positive chassis ground. 7. Install an I/O cable onto the card’s bracket mounted connector. 8. Replace the computer cover and turn ON the computer which should auto-detect the card (depending on the operating system) and automatically finish installing the drivers. 9. Run PCIfind.exe to complete installing the card into the registry (for Windows only) and to determine the assigned resources. 10. Run one of the provided sample programs that was copied to the newly created card directory (from the CD) to test and validate your installation. The base address assigned by BIOS or the operating system can change each time new hardware is installed into or removed from the computer. Please recheck PCIFind or Device Manager if the hardware configuration is changed. Software you write can automatically determine the base address of the card using a variety of methods depending on the operating system. In DOS, the PCI\SOURCE directory shows the BIOS calls used to determine the address and IRQ assigned to installed PCI devices. In Windows, the Windows sample programs demonstrate querying the registry entries (created by PCIFind and NTIOPCI.SYS during boot-up) to determine this same information. Manual PCI-AI12-16/16A 11 Chapter 3: Option Selection To operate the cards in the current mode install a jumper in the positions shown at CH0 through CH7 for each channel, 0 to 7, that you will be using as a current input. Only differential operation is supported when using current mode inputs. For best results using 4-20mA inputs, the 1.25-6.25 volt range is recommended. The CLAMP option provides a diode clamp on the Digital I/O lines, useful when switching inductive (coil) loads. Place a jumper in the CLAMP position if inductive loads will be used on DIO3-DIO0. CH0 CH7 RP1 RP2 RP3 CLAMP PGM FACTORY USE ONLY Figure 3-1: Option Selection Map Manual PCI-AI12-16/16A 12 Chapter 4: Address Selection These cards use I/O addresses offset from the selected base address assigned by the PCI bus. The address spaces are defined in the programming section of this manual. PCI architecture is Plug-and-Play. This means that the BIOS or Operating System determines the resources assigned to PCI cards rather than the user selecting those resources with switches or jumpers. As a result, you cannot set or change the card's base address or IRQ level. You can only determine what the system has assigned. To determine the base address that has been assigned, run the PCIFind.EXE utility program. This utility will display a list of all the cards detected on the PCI bus, the addresses assigned to each function on each of the cards, and the respective IRQs. Alternatively, some operating systems (Windows 95/98/2000) can be queried to determine which resources were assigned. In these operating systems, you can use either PCIFind or the Device Manager utility from the System Properties Applet of the control panel. The card is installed in the Data Acquisition class of the Device Manager list. Selecting the card, clicking Properties, and then selecting the Resources tab will display a list of the resources allocated to the card. The PCI bus supports 64K of I/O address space, so your card's addresses may be located anywhere in the 0000h to FFFFh range. PCIFind uses the Vendor ID and Device ID to search for your card, then reads the base address and IRQ. If you want to determine the base address and IRQ without using PCIFind, use the following information: The Vendor ID for these cards is 494F. (ASCII for "IO") The Device ID for the 16 is ACA8h. The Device ID for the 16(A) is ACA9h. An example of how to locate PCI card resources is provided with in the PCI\SOURCE directory, under your installation directory. This code runs in DOS, and uses the PCI defined interrupt BIOS calls to query the PCI bus for card specific information. You will need the Device ID and Vendor ID listed above to use this code. Manual PCI-AI12-16/16A 13 Chapter 5: Programming This section of the manual is divided into two parts. One part deals with programming the regular card and the second part deals with programming the A card. Programming regular card The following table shows the register definition map for the regular card. Please refer to this table as you read the subsequent descriptions of the registers. See the A section for details on that card. Offset Write Function Read Function 0* Start Conversion A/D Conversion Data, 8 Least Significant Bits 1 unused A/D Conversion Data, 4 Most Significant Bits 2* A/D Control (Channel and Range) A/D Control Readback 3 Digital Output / Sub-Mux Control Digital Output Readback 4* Option Control Option Status, Clears Interrupt 5 Digital Output (general purpose 4 bits) Digital Input (general purpose 4 bits) 6 unused unused 7 unused unused 8 8254 Counter / Timer 0 8254 Counter / Timer 0 9 8254 Counter / Timer 1 8254 Counter / Timer 1 A 8254 Counter / Timer 2 8254 Counter / Timer 2 B 8254 Counter / Timer Control 8254 Counter / Timer Status * Offsets marked with this symbol have slightly different functionality in the A card. See the next section for information on these differences. Table 5-1: Register addresses on normal card (hex) Manual PCI-AI12-16/16A 14 Register Descriptions Offset 0 Write Start Conversion This address is written to if you wish to start a conversion programmatically. Any value written to this address will cause the A/D to perform a conversion on the currently selected channel at the currently selected range. Use the A/D Control register at Offset 2 to select the channel and range. Conversions may also be started via an External Start Conversion signal (pin 4, see Offset 4) or via Counters (see Offset 4). Offset 1 Write Unused This address is unused, writes are ignored. Offset 0 Read A/D Data (Low byte) Offset 1 Read A/D Data (High nybble + SEL readback) These addresses contain the results of the most recent conversion. Data is presented in a two's complement form. Although the bytes can be read individually, coding is simplified by treating the data as a single 16-bit wide register at Offset 0. The following diagram shows the bit positions of the data returned: Read as 16-bit integer from Offset 0 Read as byte from Offset 1 Read as byte from Offset 0 sel3 sel2 sel1 sel0 Db Da D9 D8 D7 D6 D5 D4 D3 D2 D1 D0 Read a single 16-bit integer and mask off the high-order 4 bits to obtain a value. See the programming guide at the end of this chapter for more information. Sel3 through Sel0 are a readback of the state of the Sel3 through Sel0 bits as they were when the conversion was started. See Offset 3 for an explanation of the Sel bits. Offset 2 Write A/D Control Setup Channel, Range, and Single-Ended or Differential Mode. Offset 2 Read A/D Control Readback A write to this address selects the channel and range that the A/D will next convert. You must write to this register each time you wish to change the channel or range. If your program is only reading one channel and range, this register would be setup only once, during initialization. Normally, when converting more than one channel, or at more than one range, this register must be programmed before starting each conversion. Please note that a small settle time is necessary between setting this register and starting a conversion. This delay allows the channel multiplexer, the gain amplifiers, and the sample-and-hold circuitry time to settle to the new channel/range selected before the sample/hold circuit enters HOLD mode. The maximum required delay is approximately 7 microseconds. The following diagram defines bit functions in the register bit 7 bit 6 bit 5 bit 4 bit 3 bit 2 bit 1 bit 0 MA3 MA2 MA1 MA0 DIFF R2 R1 R0 MA3, MA2, MA1, MA0 These 4 bits form a binary number from 0 to 15. This is the channel number on the A/D board you wish to setup for conversion. MA3 should be cleared to zero if using Differential mode. Manual PCI-AI12-16/16A 15 DIFF This is a control bit for Single-Ended or Differential mode. In Single-Ended mode, the card has 16 channels, each converted in reference to analog ground. In Differential mode, the card has only 8 channels, and the conversion returns the voltage difference from the high to the low channel. When the bit is cleared (0), Single- Ended mode is active; a set bit (1) indicates Differential mode. R2, R1, R0 These bits select the range at which to convert the data. The following table lists the ranges and the bit combinations for each range. R2 R1 R0 Rangecode Range 0 0 0 0 bipolar 10 volts, 20 volt span-10 to +10V 0 0 1 1 bipolar 5 volts, 10 volt span-5 to +5V 0 1 0 2 bipolar 2.5 volts, 5 volt span -2.5 to +2.5V 0 1 1 3 bipolar 1.25 volts, 2.5 volt span -1.25 to +1.25V 1 0 0 4 unipolar 10 volts, 10 volt span 0 to 10V 1 0 1 5 unipolar 5 volts, 5 volt span0 to 5V 1 1 0 6 unipolar 1.25 to 3.75 volts, 2.5 volt span 1 1 1 7 unipolar 1.25 to 6.25 volts*, 5 volt span *The 1.25-6.25 volt range is designed for use with the Current Mode jumper on each channel. Selecting this range for those channels that have been placed in current mode results in a 4-20mA range, with full 12-bit precision. Reading this offset provides a readback of the current state of the register. Refer to the programming guide at the end of this chapter for more information on using this register. Offset 3 Write Digital Output / Sub Mux Control Offset 3 Read Readback This address provides seven bits of digital output. These bits can be used for any purpose, but are generally used to control the channel and range of an attached submultiplexer board, such as the AIM-16 or LVDT-8. The following table describes the register's bits and the names generally associated with Sub-Mux control bits. bit 7 bit 6 bit 5 bit 4 bit 3 bit 2 bit 1 bit 0 SEL3 SEL2 SEL1 SEL0 X G2 G1 G0 The bit X is unused. The other seven bits can be used as general purpose output bits or as Sub-Mux control. When used to control a submultiplexer, the SEL bits normally control Sub-Mux channel, and the G bits control GAIN or Range, but the exact purpose of all these bits depends on the submultiplexer used. Please refer to your submultiplexer manual for more information. The SEL3-0 bits will be returned as the top four bits when the data from the A/D converter is read to the computer. They may be used to tag the data, if they are not being used for other purposes. Manual PCI-AI12-16/16A 16 Offset 4 Write Option Control This register is used to control various features on the card. bit 7 bit 6 bit 5 bit 4 bit 3 bit 2 bit 1 bit 0 XSCE EI CTR CTR set to 1 causes start conversions to occur each time counter 2 (used in Mode 2) counts down to zero. The EI bit is Enable Interrupt. If the bit is set, each end-of-conversion generates an IRQ. Bit 7, XSCE, is External Start Conversion Enable. Setting this bit allows pin 4 on the connector to start conversions. All other bits in this register must be cleared to zero for compatibility with future options. Refer to the programming guide at the end of this chapter for more information on using this feature. Offset 4 Read Status, Clear Interrupt This register is read to determine the status of various features on the card. Primarily it is used to determine if a conversion has finished. bit 7 bit 6 bit 5 bit 4 bit 3 bit 2 bit 1 bit 0 BUSY EXT The BUSY bit indicates the conversion is in process. A zero means the A/D is busy, a one means a conversion is not in progress. This bit is one of the most important when not using interrupt modes. By reading this bit you can determine when the A/D conversion has finished and know when to take the data. The EXT bit works like a digital input bit. It shows the current state of the External Start A/D pin on the connector (pin 4). A/D conversions can be started by pulling this pin high if XSCE is set to one in Offset 4. Unused status bits are reserved for expansion and should be ignored. Offset 5 Write Digital Output, External Start Conversion Control Offset 5 Read Digital Input Four bits of general purpose I/O are provided. The least significant four bits of this register set or read the four general purpose digital I/O bits. Each I/O bit is in the input mode unless overruled by an output bit. If a bit has been set to output mode, then the input mode must be re-established by writing zeroes to the related output bits. This allows inbound data to reach the input buffer by placing the open-collector output inverters in a non- conducting state. Writing a one to the output closes the open-collector inverter, shorting the pull-up resistor network to ground and producing a low output. (Note: the status of the output may be monitored by reading the input on the same bits.) bit 7 bit 6 bit 5 bit 4 bit 3 bit 2 bit 1 bit 0 X X X X DIO3DIO2DIO1DIO0 Offset 8, 9, A and B8254 Counter / Timer Refer to the 8254 section for information on programming this device. Manual PCI-AI12-16/16A 17 Programming the A card The following table shows the registers that are different in the A version of the card. Please refer to this table as you read the subsequent descriptions of the registers. See the previous section for details on the other registers. Offset Write Function Read Function 0 Start Conversion A/D Conversion Data, 8 Least Significant Bits 1 unused A/D Conversion Data, 4 Most Significant Bits,ID 2 A/D Control (Channel and Range) A/D Control Readback 3 Digital Output / Sub-Mux Control Digital Output/Sub-Mux Control Readback 4 Option Control Option Status Register Descriptions Registers that are not shown here have exactly the same functionality as described for the base model card. Offset 0 Read A/D Data (Low byte) Offset 1 Read A/D Data (High nybble, plus Sel Readback) These addresses allow you to read the data stored in the data FIFO. The data is read oldest to newest. The format is the same as in the base model card described in the section above. The values of SEL3-0 are placed in the four most significant bits of Offset 1 and may be used as a data tag. Since the data is contained in both of these registers, it is a good practice to read Offset 0 and Offset 1 with a single command to assure that the two data registers stay properly synchronized. Offset 2&3 Write A/D Control Setup Point-List Offset 2&3 Read A/D Control Readback This address (base+2) must be written to using a 16-bit WORD command. (out dx,ax) Doing so loads the point-list FIFO. Repeated writes to this address are used to load an entire point-list into the FIFO for later use. The format of the WORD is identical to the combined format of Offset 2 and Offset 3 from the base card. (Note: it is very useful to use SEL3-SEL0 as markers, as long as external muxes are not being used, to track which channel data is from. When no external mux is being used, writing the same value to SEL3-SEL0 as MA3-MA0 causes the data FIFO to appear to hold the channel number (MA3-0), which enables easier tracking of data and channel number.) After loading up to 2048 WORDS, you must read a WORD from this address before starting conversions. Offset 4 Write Option Control This register is used to control various features on the card. bit 7 bit 6 bit 5 bit 4 bit 3 bit 2 bit 1 bit 0 XSCE CCF CF EIFH EIFE CTR The CTR bit has the same functionality as before, but its usefulness is greatly enhanced due to the presence of a point-list FIFO. CCF and CF are Clear Channel FIFO and Clear FIFO (data) respectively. When a 1 is written to these bits, the selected FIFO is reset, effectively clearing its contents. EIFH set to 1 enables interrupts to occur when the data FIFO becomes Half Full. This is the interrupt most often used in background-task-based data acquisition. The EIFE bit set to 1 enables interrupts on Error. That is, anytime the FIFO is read from when it is already empty, or when data is lost because the FIFO is full when an A/D conversion finishes. Manual PCI-AI12-16/16A 18 Offset 4 Read Status This register is read to determine the status of various features on the card, primarily the state of the point-list and data FIFOs. bit 7 bit 6 bit 5 bit 4 bit 3 bit 2 bit 1 bit 0 BUSY CFF CFH CF0 FF FH F0 EXT BUSY and EXT have the same functionality as in the base model card. CFF, CFH, CF0, FF, FH, and F0 indicate when LOW that the respective status is true. (C)FF is FIFO Full, (C)FH is FIFO Half Full, and (C)F0 means FIFO Empty. Manual PCI-AI12-16/16A 19 Programming Guide A/D Data Acquisition Taking data from an A/D can seem confusing at first, but it all boils down to a few simple steps. Set Channel and Range Offset 2 (and 3 if using SubMux) Write Start Conversion Offset 0 Write Wait for End of Conversion Offset 4 Read Read Data Offset 0 Read (16-bit integer) Repeat To set the channel, you must build the control register from its component parts. It consists of the channel, the range, and the differential or single-ended control bit. The channel is in the upper nybble, the SE/DIFF bit is next, then the range value. From the table in the programming section, you can pick the range number for the desired range, and in most programs the channel number will come from a FOR loop. Assuming the channel number is in CH, the range is in RNG, and the SE/DIFF bit is in SEDIFF, you can build a control byte with: control = (CH << 4) + (SEDIFF << 3) + RNG; This seems fairly complex, but it is made easier if you take into account that most programs will acquire data from a single range and usually at a single SE/DIFF setting. These two values, then, can be hard-coded into the program, and the code becomes: control = (ch << 4) + 1; // for Single-ended, + 5 VDC operation That is all there is for polled mode A/D conversions. The data comes back in counts, and must be converted to engineering units to be useful. The data is returned in two's complement form, but resides in only 12 bits. To get a true two's complement integer, you must sign-extend the data. The following line reads the data and converts it to the simplest form: data = ((int)inport(base + 0) << 4) >> 4; //C or C++ data := (portw[base + 0] shl 4) DIV 16;{Pascal} The variable "data" now holds a number from -2048 to 2047 for bipolar ranges, 0 to 4095 for unipolar. A simple Y = mX + b equation (where X is the data) would convert this to engineering units. Counter Driven Data Acquisition Several things change when using timed A/D start (CTR mode). Configure Counters Offset 8-B Writes Set Channel and Range Offset 2 (and 3 if using SubMux) Write Enable Counter Mode Offset 4 Write *loop Wait for Start of Conversion Offset 4 Read Set next channel and range Offset 2 (and 3 if using SubMux) Write Wait for End of Conversion Offset 4 Read Read Data Offset 0 Read (16-bit integer) Repeat at *loop Configuring the counters consists of setting up the timing for conversions using the 8254 control and load registers described in the 8254 section of this manual. Counters 1 and 2 should both be set for mode 2 operation, and the combined countdown duration of these two counters will be the delay between conversions. Manual PCI-AI12-16/16A 20 When programming channels, you must not go faster than the counters' start conversion pulses. "Wait for Start of Conversion" paces your program to the counter. "Set next channel and range" solves the need for a settle-delay between set channel and start conversion. Because only the counter knows when it is going to start a conversion, programming the channel at this step ensures as long a delay as possible is provided. Interrupt Based or Background Data Acquisition Interrupt mode adds wrinkles of it's own. Main program: Install ISR Motherboard resources Initialize interrupts Motherboard resources Configure Counters Offsets 8 through B Set Channel and Range Offset 2 Write Enable Counter & IRQ Mode Offset 4 Write Wait until done. Other code can go here. ISR: Clear Interrupt Offset 4 Read Read Data Offset 0 Read Set Channel and Range Offset 2 Write Send End-Of-Interrupt Motherboard resources Using interrupt mode requires an understanding of IRQ programming practices, such as the PIC IRQ Mask register and the IRQ vector table. Once these are grasped, however, the benefits are well worth the learning curve. IRQ mode is a great way to perform non-data gathering tasks while conversions are taking place. The background task (the ISR) takes data and stores it, while the foreground task can perform other functions (such as display, calculations, or acquisition from some other device). FIFO Based Data Acquisition Set Channel and Range FIFO Offset 2 Write 16-bit WORDS Offset 2 Read Configure Counters Offset 8-B Writes Enable Counter Mode Offset 4 Write *loop Wait for FIFO Half full Offset 4 Read Read Data until FIFO empty Offset 0 Read (16-bit integer), Offset 4 Read Loop at *loop until you have as much data as you want This mode can be used to easily test point-list setup and general FIFO functionality, but generally won't be used in real-world environments. IRQ based FIFO handling is so efficient that most applications will use that mode instead. However, many similarities exist and this mode is worthwhile as a experimental or learning aid, as debugging this mode is easier than interrupt debugging. Set Channel and Range FIFO consists of a predetermined set of WORD writes to Offset 2, setting the channel, range, and sub-mux channel and gain if used. The upper nybble (SEL3-SEL0) is returned in the upper nybble of the A/D conversion data, and is useful as a marker if no mux is to be used. If you are allowing a user to dynamically create the point-list, the Channel FIFO status bits in the Offset 4 register can warn you when the FIFO is full. Manual PCI-AI12-16/16A 21 Interrupt-Based FIFO Mode Main program: Install ISR Initialize interrupts Configure Counters Offset 8-B Writes Set Channel and Range FIFO Offset 2 Write 16-bit WORDS Offset 2 Read Enable Counter Mode Offset 4 Write Enable IRQ on FIFO Half Full (Same write as above) Wait until all the data is taken. Other code can go here. ISR: Clear Interrupt Offset 4 Read Read Data until FIFO is empty (or read ½ of FIFO size) Send End-Of-Interrupt This mode is so useful that an example is provided as part of the sample software normally installed with the card. Be aware that the card will continually interrupt on the enabled IRQ conditions while those conditions are "true". This can cause the appearance of "locking-up" a system if the IRQ handler does not remove the condition before exiting. In the case of FIFO based acquisition, this generally means reading enough data from the data FIFO that it is no longer more than half-full. Manual PCI-AI12-16/16A 22 Chapter 6: Programmable Interval Timer The card contains a type 8254 programmable counter/timer which allows you to implement such functions as a Real-Time Clock, Event Counter, Digital One-Shot, Programmable Rate Generator, Square-Wave Generator, Binary Rate Multiplier, Complex Wave Generator, and/or a Motor Controller. The 8254 is a flexible but powerful device that consists of three independent, 16-bit, presettable, down counters. Each counter can be programmed to any count between 1 or 2 and 65,535 in binary format, depending on the mode chosen. On the card these three counters are designated Counter #0, Counter #1, and Counter #2. Counter #0 is un- dedicated, with the gate, output and clock connections fully accessible via the I/O connector. Counter #0 is enabled by a discrete input and uses either the internal 1MHz clock or an external clock of up to 10MHz. Counters #1 and #2 are cascaded together to form a 32-bit counter. This dual counter can be enabled (gated) by program control and is clocked by a 1MHz precision crystal-controlled internal source. Operational Modes The 8254 modes of operation are described in the following paragraphs to familiarize you with the versatility and power of this device. For those interested in more detailed information, a full description of the 8254 programmable interval timer can be found in the Intel (or equivalent manufacturers) data sheets. The following conventions apply for use in describing operation of the 8254 : Clock: A positive pulse into the counter's clock input. Trigger: A rising edge input to the counter's gate input. Counter Loading: Programming of a binary count into the counter. Mode 0: Pulse on Terminal Count After the counter is loaded, the output is set low and will remain low until the counter decrements to zero. The output then goes high and remains high until a new count is loaded into the counter. A trigger enables the counter to start decrementing. This mode is commonly used for event counting with Counter #0. Mode 1: Retriggerable One-shot The output goes low on the clock pulse following a trigger to begin the one-shot pulse and goes high when the counter reaches zero. Additional triggers result in reloading the count and starting the cycle over. If a trigger occurs before the counter decrements to zero, a new count is loaded. Thus, this forms a re-triggerable one-shot. In mode 1, a low output pulse is provided with a period equal to the counter count-down time. Mode 2: Rate Generator This mode provides a divide-by-N capability where N is the count loaded into the counter. When triggered, the counter output goes low for one clock period after N counts, reloads the initial count, and the cycle starts over. This mode is periodic, the same sequence is repeated indefinitely until the gate input is brought low. This mode is used on the card in Counters #1 and #2 to generate periodic A/D start commands. This mode also works well as an alternative to mode 0 for event counting. Mode 3: Square Wave Generator This mode operates periodically like mode 2. The output is high for half of the count and low for the other half. If the count is even, then the output is a symmetrical square wave. If the count is odd, then the output is high for (N+1)/2 counts and low for (N-1)/2 counts. Periodic triggering or frequency synthesis are two possible applications for this mode. Note that in this mode, to achieve the square wave, the counter decrements by two for the total loaded count, then reloads and decrements by two for the second part of the wave form. Manual PCI-AI12-16/16A 23 Mode 4: Software Triggered Strobe This mode sets the output high and, when the count is loaded, the counter begins to count down. When the counter reaches zero, the output will go low for one input period. The counter must be reloaded to repeat the cycle. A low gate input will inhibit the counter. This mode can be used to provide a delayed software trigger for initiating A/D conversions. Mode 5: Hardware Triggered Strobe In this mode, the counter will start counting after the rising edge of the trigger input and will go low for one clock period when the terminal count is reached. The counter is retriggerable. The output will not go low until the full count after the rising edge of the trigger. Programming On the card, the 8254 counters occupy the following addresses: Base Address + 8: Read/Write Counter #0 Base Address + 9: Read/Write Counter #1 Base Address + A: Read/Write Counter #2 Base Address + B: Write to Counter Control register The counters are programmed by writing a control byte into a counter control register at Base Address + F. The control byte specifies the counter to be programmed, the counter mode, the type of read/write operation, and the modulus. The control byte format is as follows: Base + B Write: Counter Control Byte B7 B6 B5 B4 B3 B2 B1 B0 SC1 SC0 RW1 RW0 M2 M1 M0 BCD SC0-SC1: These bits select the counter that the control byte is destined for. SC1 SC0 Function 0 0 Program Counter #0 0 1 Program Counter #1 1 0 Program Counter #2 1 1 Read/Write Cmd.* * See section on Reading and Loading the Counters. Manual PCI-AI12-16/16A 24 RW0-RW1: These bits select the read/write mode of the selected counter. RW1 RW0 Counter Read/Write Function 0 0 Counter Latch Command 0 1 Read/Write LS Byte 1 0 Read/Write MS Byte 1 1 Read/Write LS Byte, then MS Byte M0-M2: These bits set the operational mode of the selected counter. Mode M2 M1 M0 0 0 0 0 1 0 0 1 2 X 1 0 3 X 1 1 4 1 0 0 5 1 0 1 BCD: Set the selected counter to count in binary (B0 = 0) or BCD (B0 = 1). Reading and Loading the Counters If you attempt to read the counters on the fly when there is a high input frequency, you will most likely get erroneous data. This is partly caused by carries rippling through the counter during the read operation. Also, the low and high bytes are read sequentially rather than simultaneously and, thus, it is possible that carries will be propagated from the low to the high byte during the read cycle. To circumvent these problems, you can perform a counter-latch operation in advance of the read cycle. To do this, load the RW1 and RW2 bits with zeroes. This instantly latches the count of the selected counter(selected via the SC1 and SC0 bits) in a 16-bit hold register. (An alternative method of latching counter(s) which has an additional advantage of operating simultaneously on several counters is by use of a readback command to be discussed later.) A subsequent read operation on the selected counter returns the held value. Latching is the best way to read a counter on the fly without disturbing the counting process. You can only rely on directly read counter data if the counting process is suspended while reading, by bringing the gate low, or by halting the input pulses. For each counter you must specify in advance the type of read or write operation that you intend to perform. You have a choice of loading/reading (a) the high byte of the count, or (b) the low byte of the count, or (c) the low byte followed by the high byte. This last is of the most general use and is selected for each counter by setting the RW1 and RW0 bits to ones. Of course, subsequent read/load operations must be performed in pairs in this sequence or the sequencing flip-flop in the 8254 chip will get out of step. Manual PCI-AI12-16/16A 25 Base + B Read: Counter Control Byte B7 B6 B5 B4 B3 B2 B1 B0 1 1 CNT STA C2 C1 C0 0 CNT: When is 0, latches the counters selected by bits C0-C2. STA: When is 0, returns the status byte of counters selected by C0-C2. C0, C1, C2: When high, select a particular counter for readback. C0 selects Counter 0, C1 selects Counter 1, and C2 selects Counter 2. You can perform two types of operations with the Counter Control Byte. When CNT=0, the counters selected by C0 through C2 are latched simultaneously. When STA=0, the counter status byte is read when the counter I/O location is accessed. The counter status byte provides information about the current output state of the selected counter and its configuration. The status byte returned if STA=0 is: B7 B6 B5 B4 B3 B2 B1 B0 OUT NC RW1 RW2 M2 M1 M0 BCD OUT: Current state of counter output pin. NC: Null count. This indicates when the last count loaded into the counter register has actually been loaded into the counter itself. The exact time of load depends on the configuration selected. Until the count is loaded into the counter itself, it cannot be read. RW1 & RW0: Read/Write command. M2, M1, M0: Counter mode. BCD: BCD = 0 is binary mode, otherwise counter is in BCD mode. If both STA and CNT bits in the counter status byte are set low and the RW1 and RW0 bits have both been previously set high in the counter control register (thus selecting two-byte reads), then reading a selected counter address location will yield: 1st Read: Status byte 2nd Read: Low byte of latched data 3rd Read: High byte of latched data After any latching operation of a counter, the contents of its hold register must be read before any subsequent latches of that counter will have any effect. If a status latch command is issued before the hold register is read, then the first read will read the status, not the latched value. In this case, the latched value may be read after reading the status. Manual PCI-AI12-16/16A 26 Programming Examples Generating a Square Wave Output To program Counters #1 and #2 for a 1 KHz output you need to divide the 1MHz crystal oscillator input by 1,000. To obtain a symmetrical waveform, the divisor loaded into the counter should be an even number. If it is an odd number, then one half of the waveform would be one input clock pulse period longer than the other. A convenient divisor to use in counter #1 is 10 and counter #2 is 100 (because 10 x 100 = 1,000). outportb(BASEADDRESS + B, 0x76); /* counter #1 to square wave mode */ outportb(BASEADDRESS + B, 0xb6); /* counter #2 to square wave mode */ outportb(BASEADDRESS + 9,10); /* write lower byte, counter #1 */ outportb(BASEADDRESS + 9,0); /* write upper byte, counter #1 */ outportb(BASEADDRESS + A,100); /* write lower byte, counter #2 */ outportb(BASEADDRESS + A,0); /* write upper byte, counter #2 */ Using Counter #0 as a Pulse Counter Since the counters are "down" counters the resulting count is subtracted from the starting value to determine the number of pulses. This example starts with a value of 65,535: outportb(BASEADDRESS + B,0x30); /* counter #0, mode 0 */ outportb(BASEADDRESS + 8,0xff); /* counter #0 low load byte */ outportb(BASEADDRESS + 8,0xff); /* counter #0 high load byte */ Measuring Frequency and Period The two previous sections show how to count pulses and generate output frequencies. It is also possible to measure frequency by raising the gate input of Counter 0 for a known time interval and counting the number of clock pulses accumulated for that interval. The gating signal can be derived from Counters #1 and #2 operating in a square wave mode. Counter #0 can also be used to measure pulse width or half period of a periodic signal. The signal should be applied to the gate input of Counter #0 and a known frequency (such as the 1MHz crystal controlled oscillator) applied to the Counter #0 clock input. During the interval when the gate input is low, Counter #0 is loaded with a full count of 65,535. When the gate input goes high, the counter begins decrementing until the gate input goes back low at the end of the pulse. The counter is then read and the change in count is a linear function of the duration of the gate input signal. Longer pulse durations can be measured if Counters #1 and #2 are used as the input clock source for Counter #0, or by using an external clock source. Generating Time Delays There are four methods of using Counter #0 to generate programmable time delays. Pulse on Terminal Count After loading, the counter output goes low. Counting is enabled when the gate goes high. The counter output will remain low until the count reaches zero, at which time the counter output goes high. The output will remain high until the counter is reloaded by a programmed command. If the gate goes low during countdown, counting will be disabled as long as the gate input is low. Programmable One-Shot The counter need only be loaded once. The time delay is initiated when the gate input goes high. At this point the counter output goes low. If the gate input goes low, counting continues but a new cycle will be initiated if Manual PCI-AI12-16/16A 27 the gate input goes high again before the timeout delay has expired; i.e., is re-triggerable. At the end of the timeout, the counter reaches zero and the counter output goes high. That output will remain high until re- triggered by the gate input. Software Triggered Strobe This is similar to Pulse-on-Terminal-Count except that, after loading, the output goes high and only goes low for one clock period upon timeout. Thus, a negative strobe pulse is generated a programmed duration after the counter is loaded. Hardware Triggered Strobe This is similar to Programmable-One-Shot except that when the counter is triggered by the gate going high, the counter output immediately goes high, then goes low for one clock period at timeout, producing a negative-going strobe pulse. The timeout is re-triggerable; i.e., a new cycle will commence if the gate goes high before a current cycle has timed out. Generating Interrupts with the Counter/Timer The card’s architecture allows you to directly generate an interrupt upon an ADC end of conversion or the timeout of Counter #2. This allows you to either read the converted data or use the counter while using external start of conversions. Note also that it is possible to trigger the A/D externally or by a programmed write to an I/O port and invoke an interrupt at the end of A/D conversion in the same way. Manual PCI-AI12-16/16A 28 Chapter 7: Calibration The cards are calibrated through a software routine contained in the setup program. Once the card is setup, run the calibration sequence as shown in the program and make the calibration adjustments on RP1, RP2, and RP3 on the board. Manual PCI-AI12-16/16A 29 Chapter 8: Connector Pin Assignments The analog inputs are accessible via a male 37-pin D type connector that extends through the back of the computer case and a DB37S solder cup plug may be used to make connections. Pin Name Function 1 VDD +12VDC Power from the Computer Bus 2 CLK0 Counter 0 Clock Input 3 G0 LSBit of AIM-16P Gain Select Bits 4 EXT External Start Conversion Source Pin 5 G1 Bit 1 of AIM-16P Gain Select Bits 6 G2 MSBit of AIM-16P Gain Select Bits 7 SEL0 Multiplexer Channel Selection Bit LSBit 8 SEL1 Multiplexer Channel Selection Bit 9 SEL2 Multiplexer Channel Selection Bit 10 SEL3 Multiplexer Channel Selection MSBit 11 DGround Digital Ground 12 GATE1 Counter/Timer Gate Pulse 13 OUT2 Counter/Timer 2 Counter Output 14 DI/O 0 Digital I/O LSB 15 DI/O 1 Digital I/O Bit 16 DI/O 2 Digital I/O Bit 17 IN8- Chl 7 Analog Low Input (Diff’l) Chl 15 Analog High Input (SE) 18 AGround Low Level Analog Common Ground 19 VREF +10VDC Reference Voltage 20 VSS -12VDC 21 IN7- Chl 6 Analog Low Input (Diff’l) Chl 14 Analog High Input (SE) 22 IN6- Chl 5 Analog Low Input (Diff’l) Chl 13 Analog High Input (SE) 23 IN5- Chl 4 Analog Low Input (Diff’l) Chl 12 Analog High Input (SE) 24 IN4- Chl 3 Analog Low Input (Diff’l) Chl 11 Analog High Input (SE) 25 IN3- Chl 2 Analog Low Input (Diff’l) Chl 10 Analog High Input (SE) 26 IN2- Chl 1 Analog Low Input (Diff’l) Chl 9 Analog High Input (SE) 27 IN1- Chl 0 Analog Low Input (Diff’l) Chl 8 Analog High Input (SE) 28 DI/O 3 Digital I/O MSB 29 +5VDC +5VDC Power from Computer Bus 30 IN8 Chl 7 Analog High Input 31 IN7 Chl 6 Analog High Input 32 IN6 Chl 5 Analog High Input 33 IN5 Chl 4 Analog High Input 34 IN4 Chl 3 Analog High Input 35 IN3 Chl 2 Analog High Input 36 IN2 Chl 1 Analog High Input 37 IN1 Chl 0 Analog High Input Table 7-1: Connector Pin Assignments Manual PCI-AI12-16/16A 30 Customer Comments If you experience any problems with this manual or just want to give us some feedback, please email us at: tech@portwell.com. Please detail any errors you find and include your mailing address so that we can send you any manual updates. Manual PCI-AI12-16/16A 31
Frequently asked questions
Why choose IPC Station?

What is IPC Station' warranty policy for the PCI-AI12-16A?

What carriers does IPC Station use to ship parts?

Does IPC Station sell to international (non-USA) customers?

What methods of payment does IPC Station accept?

Why buy from GID?
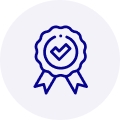
Quality
We are industry veterans who take pride in our work
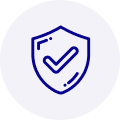
Protection
Avoid the dangers of risky trading in the gray market
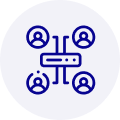
Access
Our network of suppliers is ready and at your disposal

Savings
Maintain legacy systems to prevent costly downtime
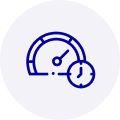
Speed
Time is of the essence, and we are respectful of yours
Related Products

Low Profile single port asynchronous serial communication card that can be installed in any 3.3V or ...
What they say about us
FANTASTIC RESOURCE
One of our top priorities is maintaining our business with precision, and we are constantly looking for affiliates that can help us achieve our goal. With the aid of GID Industrial, our obsolete product management has never been more efficient. They have been a great resource to our company, and have quickly become a go-to supplier on our list!
Bucher Emhart Glass
EXCELLENT SERVICE
With our strict fundamentals and high expectations, we were surprised when we came across GID Industrial and their competitive pricing. When we approached them with our issue, they were incredibly confident in being able to provide us with a seamless solution at the best price for us. GID Industrial quickly understood our needs and provided us with excellent service, as well as fully tested product to ensure what we received would be the right fit for our company.
Fuji
HARD TO FIND A BETTER PROVIDER
Our company provides services to aid in the manufacture of technological products, such as semiconductors and flat panel displays, and often searching for distributors of obsolete product we require can waste time and money. Finding GID Industrial proved to be a great asset to our company, with cost effective solutions and superior knowledge on all of their materials, it’d be hard to find a better provider of obsolete or hard to find products.
Applied Materials
CONSISTENTLY DELIVERS QUALITY SOLUTIONS
Over the years, the equipment used in our company becomes discontinued, but they’re still of great use to us and our customers. Once these products are no longer available through the manufacturer, finding a reliable, quick supplier is a necessity, and luckily for us, GID Industrial has provided the most trustworthy, quality solutions to our obsolete component needs.
Nidec Vamco
TERRIFIC RESOURCE
This company has been a terrific help to us (I work for Trican Well Service) in sourcing the Micron Ram Memory we needed for our Siemens computers. Great service! And great pricing! I know when the product is shipping and when it will arrive, all the way through the ordering process.
Trican Well Service
GO TO SOURCE
When I can't find an obsolete part, I first call GID and they'll come up with my parts every time. Great customer service and follow up as well. Scott emails me from time to time to touch base and see if we're having trouble finding something.....which is often with our 25 yr old equipment.
ConAgra Foods